Skip Ahead:
It’s a new year, which means fresh production and revenue goals to achieve. As you plan your approach to meet these goals, consider these strategies to streamline your operations and enhance your success.
Making the most of monitoring
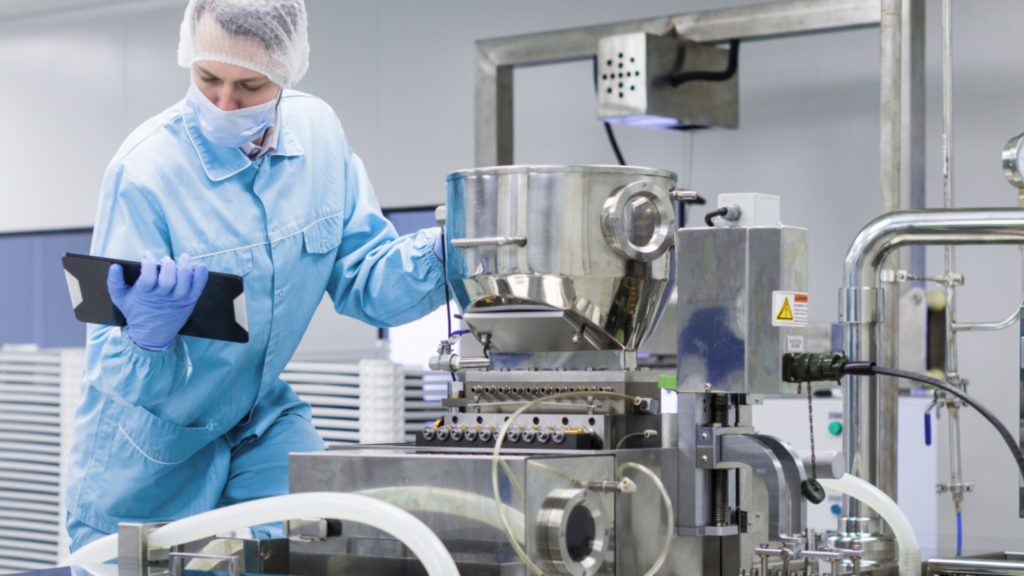
Many pharmaceutical manufacturers do not realize that they’re sitting on a goldmine of useful data from their equipment. This data, such as temperature and pressure readings, counters, and vibrational measurements can significantly enhance both operational efficiency and product quality.
A good rule of thumb is if your equipment monitors it, it can also report on it.
Your equipment monitors valuable data that can be used for predictive maintenance. By setting up systems that alert you when key measurements stray from acceptable ranges or begin to trend away from your target, you can address issues and schedule maintenance before they lead to equipment failures and disrupt production.
Additionally, this data can help you pinpoint areas where your processes may be lacking. Reporting on process steps can help you identify areas where your equipment might be over or under correcting, allowing you to to adjust production tolerances for a more seamless production process.
In Summary: You can implement automated reporting and alarm systems in your production process to turn raw data into actionable insights, helping to improve maintenance schedules and overall manufacturing efficiency.
Build an industrial network
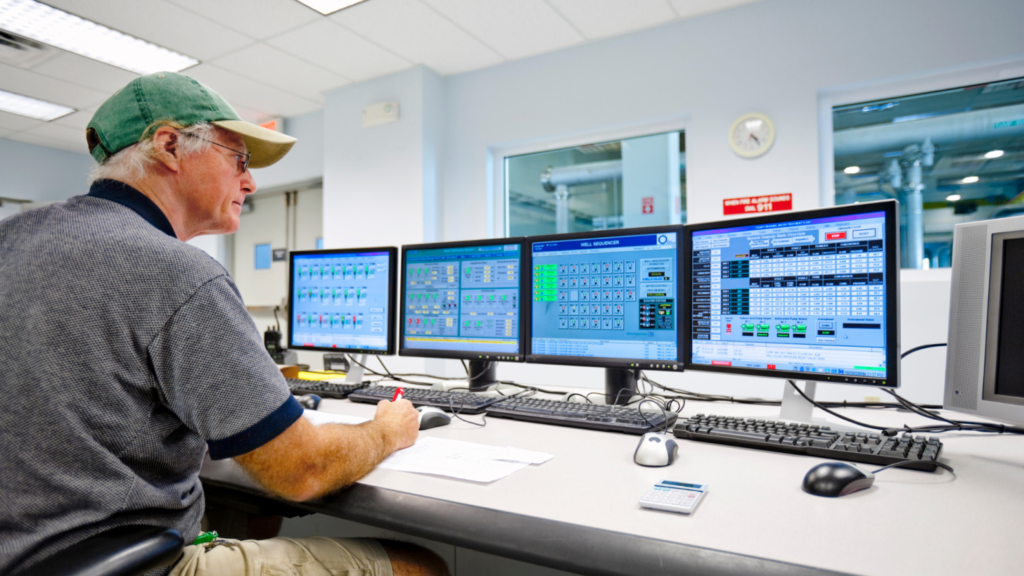
Effective communication is crucial for smooth operations, and this holds true for your industrial equipment as well. Many manufacturing setups involve complex machinery sourced from various suppliers. If these machines operate independently without intercommunication, it can lead to frustrating delays and pose security risks.
Integrating all data monitoring for a production process into a single control room enables seamless communication between different pieces of equipment. This centralization also allows for real-time reporting, enabling management to monitor and manage production processes more effectively.
With an industrial network, you can easily see what equipment is running and how production is progressing. This data can be fed into a desktop application, giving management a continuous, real-time overview without the need to frequently check in manually. This setup enhances both safety and security, allowing for monitoring that’s accessible right from your fingertips. You can customize access levels, from viewing on mobile devices or tablets from home to restricting access to desktops connected to the company’s Wi-Fi network.
Every monitored parameter, be it temperature, pressure, or counts, is reported back to the control desk, ensuring that every aspect of the production process is under constant surveillance. This integration not only improves oversight but also boosts overall production efficiency.
In Summary: Integrating all equipment data into a single control room streamlines communication and real-time reporting across various machines, significantly enhancing management oversight, safety, and the efficiency of drug production processes.
Integrate your systems
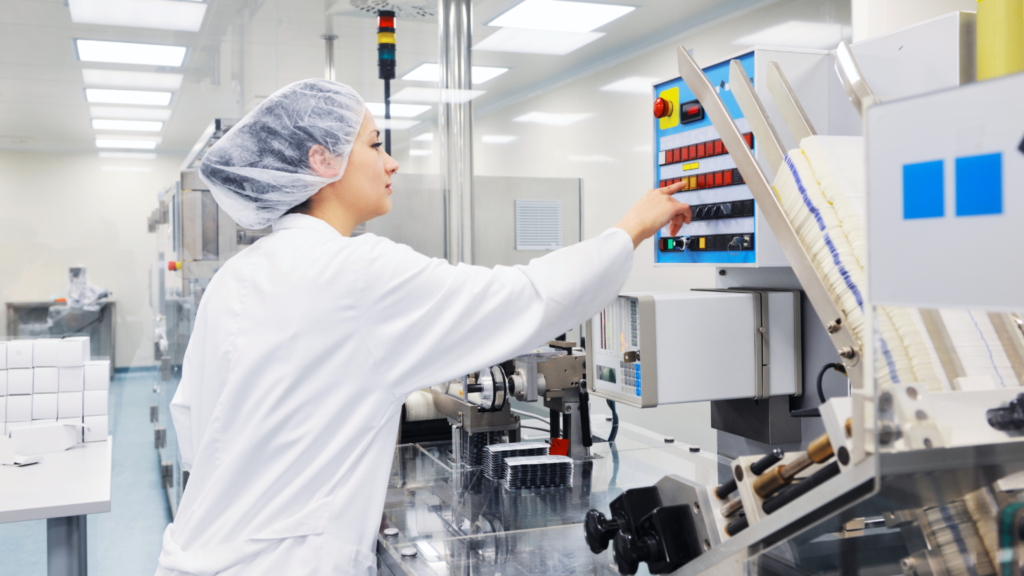
Once you have a centralized control room that consolidates equipment monitoring, you unlock the potential to not just watch but actively coordinate your systems. Integrating your equipment allows the equipment to not only self-monitor but also to respond to the conditions of other machines in real-time.
For instance, consider an aseptic filling line that conducts weight checks every 100 units. You can configure downstream equipment to only process units one they have been bracketed by a passing weight check. Similarly, a basic bottling line can be set to pause operations and signal operators to replenish materials if a pill count is low.
Moreover, equipment can be programmed to make adjustments itself. For example, should a weight check exceed an action limit, the system can either halt operations and notify staff to make necessary adjustments, or automatically recalibrate and record the changes to be included in the batch record at the end of the production cycle.
Integrating your equipment in this manner optimizes the entire manufacturing process, enhancing quality and reducing production time by ensuring that each component operates in harmony with the others.
In Summary: A centralized control room offers not just monitoring but also real-time coordination of equipment, allowing machines to interact and respond to each other’s conditions, ensuring that all components work together efficiently.
Seamless operations deliver more
Every business operates differently. We work closely with our clients to understand their unique processes. Our goal is to tailor and adjust their systems for improved production, quality, and return on investment.
If you stick with the default settings that come with your equipment, you’re likely not using it to its full potential. Instead of just running your machines based on what the manufacturer sets, we can customize them to anticipate and react to your production needs.
If you want to learn how PharmaPhixx can help customize your equipment and streamline your business, reach out to us, and let’s talk!